APQP and it use
The Advanced Product Quality Planning (APQP) is a structured approach that helps organizations ensure that their products meet customer requirements and expectations. It is a framework that enables businesses to plan, develop, and launch new products or make changes to existing ones in a systematic and efficient manner. APQP is widely used in the automotive industry but can be applied to any sector that requires a high level of quality assurance.
Benefits of APQP
Implementing APQP offers several benefits to organizations. First and foremost, it helps in reducing the risk of product failures or defects. By following a structured process, potential issues can be identified and addressed early on, minimizing the chances of costly recalls or customer dissatisfaction.
APQP also promotes collaboration and communication among cross-functional teams. It encourages different departments, such as engineering, manufacturing, and quality assurance, to work together from the early stages of product development. This collaboration ensures that all aspects of the product are considered and that potential problems are identified and resolved collectively.
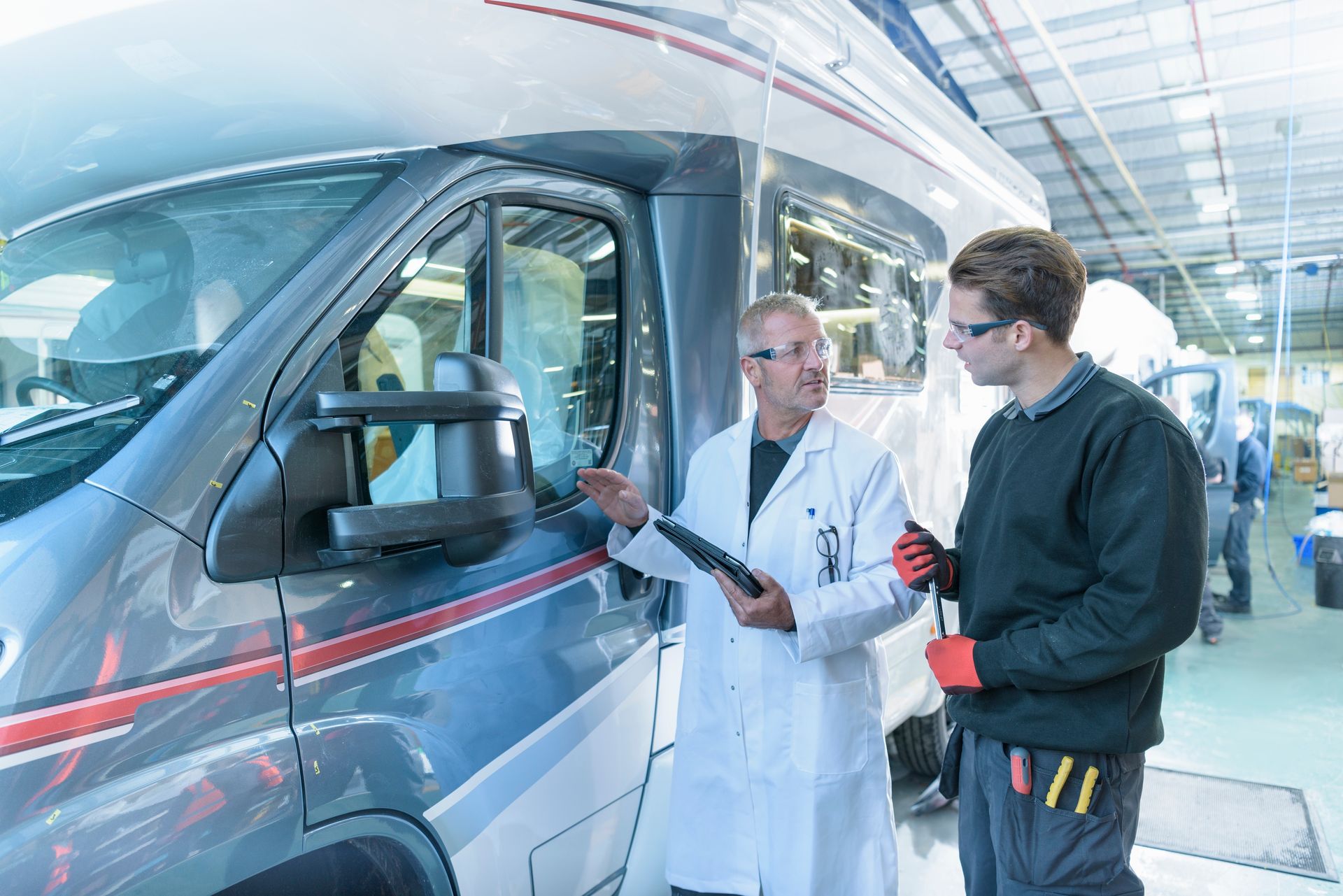
The APQP Process
The APQP process consists of several phases, each with its specific activities and deliverables. These phases include:
- Planning and defining the program
- Product design and development
- Process design and development
- Product and process validation
- Product launch and production
- Feedback, assessment, and corrective actions
Throughout these phases, organizations use various tools and techniques to ensure that every aspect of the product meets the required quality standards. These tools may include Failure Mode and Effects Analysis (FMEA), Control Plans, and Statistical Process Control (SPC).
Implementing APQP
Implementing APQP requires a commitment from the top management and the involvement of all relevant departments. It is essential to allocate resources and provide training to employees to ensure they understand the APQP process and their roles within it.

Key Steps in Implementing APQP
1. Establish a cross-functional APQP team: Bring together representatives from different departments to form a team responsible for implementing APQP.
2. Define customer requirements: Understand the needs and expectations of the customers to ensure the product is designed and developed to meet those requirements.
3. Develop a detailed project plan: Create a project plan that outlines the activities, timelines, and responsibilities for each phase of the APQP process.
4. Conduct risk assessments: Identify potential risks and develop contingency plans to mitigate them. This may involve conducting FMEA and other risk analysis techniques.
5. Monitor and measure progress: Regularly review the project's progress and measure key performance indicators to ensure that the project is on track.
Conclusion
APQP is a valuable tool for organizations looking to ensure the quality of their products and minimize the risk of failures or defects. By following a structured approach and involving cross-functional teams, businesses can improve collaboration, identify and address potential issues early on, and ultimately deliver products that meet customer expectations.